Managing a warehouse means ensuring that lifting operations are safe, efficient, and reliable. But choosing the right electric chain hoist can feel overwhelming, given the options. The wrong choice could lead to inefficiencies or even safety hazards. This guide will walk you through the essential factors to consider for a smart, informed purchase.
When buying an electric chain hoist for your warehouse, prioritize factors such as load capacity, duty cycle, lifting speed, power supply compatibility, and essential safety features. Also, consider the durability, brand reputation, and warranty, alongside your specific operational needs, like work environment and operator comfort.
Now, let’s break down these considerations to ensure your electric chain hoist perfectly matches your warehouse’s demands.
How Do I Choose a Hoist?
I once tried lifting a heavy engine block using an old hoist in my workshop. It took forever. I realized I needed the right equipment. Is there a simple way to pick a proper hoist?
Choosing a hoist involves matching the load capacity, choosing the best suspension, making sure the duty class fits your usage, and picking a lifting speed that won’t slow you down. These four factors shape safety, efficiency, and equipment lifespan.
I remember how nerve-wracking it was when I heard the old hoist creak. That moment taught me the value of picking a reliable, well-suited hoist. Let’s dig deeper into the core considerations.
Understanding Capacity
I discovered that capacity is crucial for safety. I always check the maximum load a hoist can handle before buying.
A safe rule is to choose a hoist with room to spare—about 10–15% above your heaviest load. If your load hovers between two sizes, I pick the higher capacity.
I learned that the Mean Effective Load (MEL) matters for electric or pneumatic hoists. If I lift items close to the max all day, the hoist endures more strain. This concept helps me avoid overworking the motor.
Why Capacity Margin Matters
A small buffer prevents frequent overload. It reduces strain on the mechanics.
Mean Effective Load (MEL)
Some hoists handle repeated heavy lifts better. Check specs for MEL if I run the hoist at near-max loads often.
Load Factor | Recommended Action |
---|---|
Just at max | Use hoist with ~10–15% higher capacity |
Frequent heavy use | Consider MEL for better long-term service |
Choosing a Suspension Type
I found that where and how I install the hoist changes the type of suspension I need.
Hook-mounted hoists offer flexibility, while lug-mounted hoists bring extra stability. Each style fits different setups and load movements.
I watch for the mounting environment. A hook-mount is simple if I move equipment around. Lug-mount works for a permanent beam or trolley.
Hook-Mounted Hoists
They attach quickly to a beam or crane hook. They suit mobile or multi-station tasks.
Lug-Mounted Hoists
They bolt directly to a beam or trolley. They provide a solid, permanent setup.
Understanding Duty Class
I remember discovering duty class ratings, labeled from H1 to H6. That rating shows how often and how hard the hoist can work.
Lighter classes handle fewer lifts per day. Heavier classes manage tougher tasks and higher loads more frequently.
I check how many lifts I’ll do each hour and how long each lift lasts. Harsh environments or constant use demand a heavier duty class.
Frequency of Use
More lifts in a day require a robust duty class.
Environment
Dusty areas or high heat push me to choose a more durable model.
Selecting the Right Lifting Speed
I noticed that slow hoists seemed too sluggish, while very fast ones sometimes felt risky.
High-speed hoists cut downtime but can reduce control. Slow speeds add precision, helpful for delicate lifts.
I weigh time requirements against safety. If I raise loads often, a faster hoist helps productivity. If I need exact positioning, a slower speed is safer.
Faster Speeds
Useful for large projects where quick turnaround is key.
Slower Speeds
Ideal for fragile items or when I must carefully align parts.
How Do I Choose Common Rated Capacities for Electric Chain Hoists?
I once felt unsure about what size hoist to buy for my warehouse. My worry was that I might buy one too weak for certain loads or too big for my limited space.
Electric chain hoists typically span from 0.125 tons (250 lbs) to over 50 tons (100,000 lbs). Light-duty models (around 1/8 ton) handle small items. Heavier units (5 tons and up) lift bulky loads often found in large warehouses or factories.
I remember lifting a 2-ton crate with an undersized hoist. It stalled and made me nervous. That experience taught me to match the rated capacity to my actual needs. Let’s explore common hoist sizes and examples.
Understanding Common Rated Capacities
I noticed that electric chain hoists come in various capacities. This part shows their typical ranges and explains how they fit warehouse tasks.
The smallest units lift about 1/8 ton. Large industrial hoists can exceed 50 tons. My choice depends on the heaviest load I plan to move.
I believe it helps to break them into groups. Light loads hover below 1 ton. Medium loads go from 1 to 3 tons. Heavy loads can reach 5, 10, or even 20 tons. Some specialized systems top 50 tons or more.
Below is a simple table illustrating common capacity brackets:
Capacity Range | Typical Uses |
---|---|
0.125 – 0.5 tons | Light parts, small packages |
1 – 3 tons | Pallets, medium crates |
5 – 10 tons | Larger machinery, bulk materials |
20 – 50+ tons | Heavy industrial components |
Examples for Warehouse Use
Starke Variable Speed Hoist
I saw units ranging from 1/2 ton up to 3 tons. These work well for busy warehouse stations. The variable speed setting helps control the lift when dealing with fragile items.
CM Lodestar
I noticed this brand often covers 1/8 ton to 20 tons. It is a familiar choice for general warehouse duties, from lifting small boxes to hefting large bins.
Demag DC-Com
I recall seeing a lighter series that handles up to about 0.1375 tons (275 lbs). It is ideal for precise tasks, like carefully positioning items on shelves.
Harrington Electric Chain Hoists
They have a broad range from 1/8 ton up to 20 tons. That means I can pick a lightweight model for occasional lifts or a tougher version for frequent big loads.
Why Is Lifting Speed and Duty Cycle Important?
I once faced a time crunch on a job site. My hoist felt slow, and the queue of loads started piling up. That day, I realized that both lifting speed and duty cycle make or break efficiency.
Lifting speed decides how fast loads move, raising throughput. Duty cycle, meanwhile, shows how often equipment can run without overheating or wearing out. Balancing these two factors saves time, cuts costs, and avoids breakdowns.
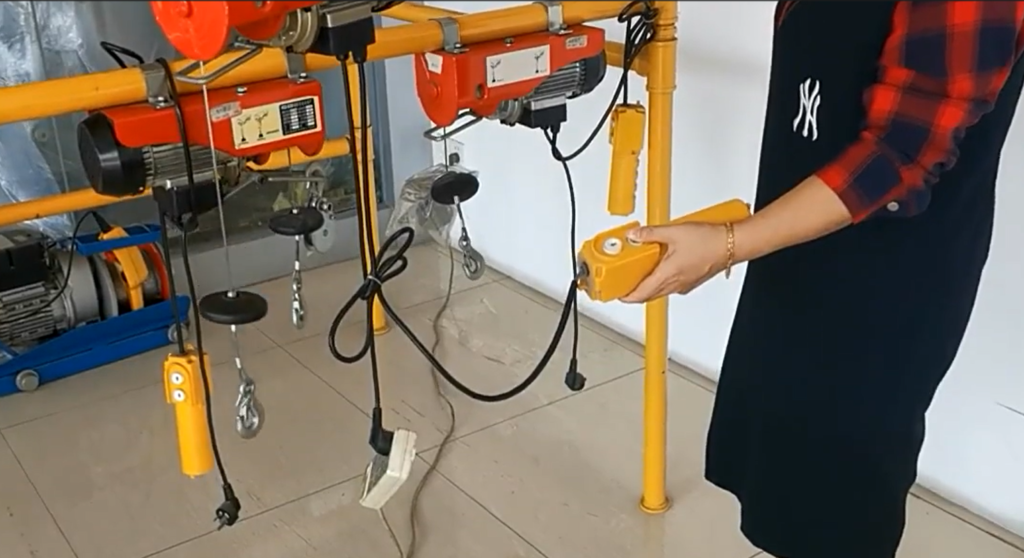
I remember watching a coworker push a hoist beyond its limit. It overheated, and we lost precious hours waiting for it to cool down. That sparked my interest in how lifting speed and duty cycle affect daily operations.
Understanding Lifting Speed
I used to think faster hoists always meant more productivity. It seemed logical, but I learned there are pros and cons.
High speeds let us handle more lifts in less time, boosting output. Yet, rushing can cause jerky moves, raising accident risks. A balanced speed keeps operations smooth and safe.
I see the effect in busy warehouses. Workers want quick lifts. But if the speed is too high, loads swing dangerously, risking product damage. In delicate tasks, slower speeds give better control. I realized picking the right speed depends on my specific load type and handling needs.
Understanding Duty Cycle
I first heard “duty cycle” and thought it was just another spec. Then I discovered it’s crucial for a hoist’s lifespan.
Duty cycle measures how often the hoist can run without overheating. If I exceed the recommended workload, I risk breakdowns and more frequent maintenance.
I noticed that heavy-duty rated hoists handle non-stop lifting all day. Light-duty models struggle under constant loads. By matching a hoist’s duty cycle to real-world use, I avoid costly downtime. I also keep operators safer and more productive.
How Do I Inspect a Chain Hoist?
I once overlooked a minor bend in my chain hoist. I thought it was no big deal. Later, I realized that small damage can quickly grow into a huge safety risk.
Regular inspections save me from costly failures. I look for any deformation, wear, dryness of lubrication, or broken strands. These issues hint at a weakened chain that might snap under load.
I remember the day my chain hoist made an odd clunk sound. That noise pushed me to learn proper inspection steps. Let me share the key tips I now follow.
Understanding Deformation
I have seen chains get twisted or bent over time. Even small distortions matter a lot.
A bent link won’t carry weight properly. That link could snap under strain. I also measure the overall chain length to catch any unexpected stretch.
When checking for deformation, I lay out the chain on a flat surface. I look for any link that isn’t aligned. A big clue is a link that appears thicker on one side. I replace that section if I see any distortion.
Visual Signs of Deformation
- Twisted or bent links
- Swollen or uneven metal
- Chain length out of spec
Understanding Wear
I learned that wear often hides in the inner corners of the chain links. It can be easy to miss.
Nicks, shiny areas, or rough spots show friction. Any deep groove can weaken the link. If wear is bad, I swap out the chain.
I clean the chain first. Grease and dirt hide small cracks. After cleaning, I check each link under good light. A gauge or caliper helps confirm if the metal lost thickness. If it’s outside the recommended range, I set the chain aside.
Common Wear Clues
Indicator | Possible Cause |
---|---|
Shiny patches | Excess friction / dryness |
Nicks or gouges | Impact or rough handling |
Reduced thickness | Ongoing abrasion |
Understanding Lubrication
I once ran a chain hoist dry, thinking it was no big deal. That mistake wore the chain out fast.
Lubrication reduces friction. A dry chain grinds itself down, making it prone to sudden breaks.
I always wipe off heavy grime first. Then I apply a proper chain lube. If the chain is extremely dirty, I soak it in a cleaner, wipe it thoroughly, and inspect for damage before lubricating.
Tips for Lubrication
- Use the correct lubricant
- Clean the chain thoroughly
- Apply oil or grease consistently
- Remove excess to prevent dirt buildup
Understanding Broken Strands
Broken or cracked links are major red flags. They might not survive another lift.
I look for any fractured metal on the surface. One broken link can compromise the entire hoist.
I run my fingers along the chain to feel for sharp edges or cracks. If a link is cracked, I never risk a temporary fix. I replace it right away. Reeving the load chain correctly also helps avoid repeated stress in the same spots.
Load Chain Reeving Checks
- Ensure no kinks
- Check alignment with the hoist sprocket
- Keep tension even across the chain
What Safety Features Should a Warehouse Hoist Have?
I once saw a hoist stall with a heavy load, and it was alarming. That close call showed me how vital safety features are for warehouse hoists.
A well-equipped warehouse hoist typically has overload protection, a clearly accessible emergency stop (E-STOP), and recognized safety certifications. These components prevent mechanical failures, help operators respond quickly to danger, and confirm that the hoist meets rigorous industry standards.
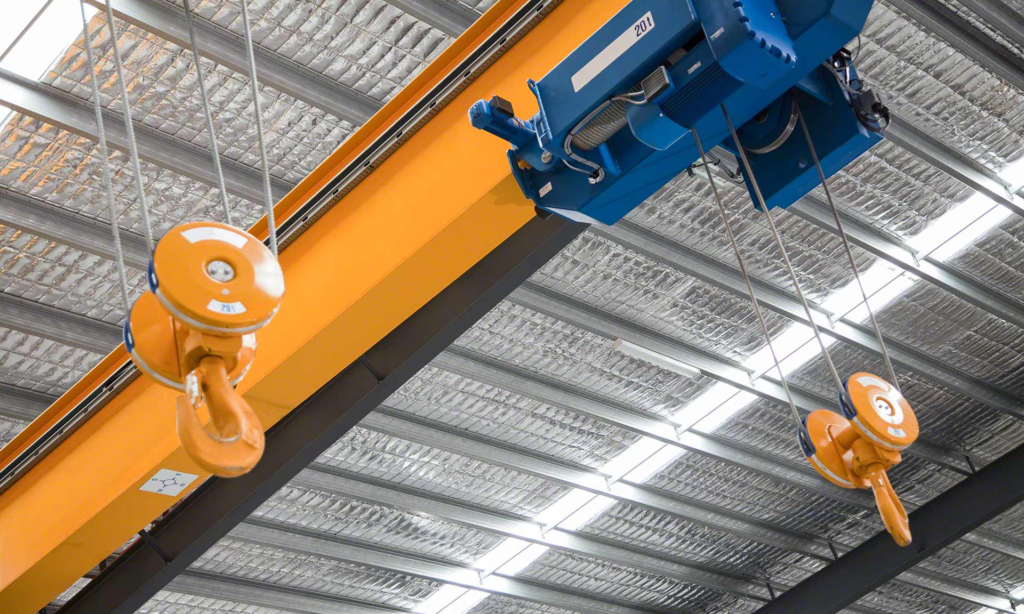
I remember how relieved I felt when I pressed an E-STOP button during a test run. That immediate stop saved us from damaged goods and possible injuries. Let’s look at these key safety features more closely.
Overload Protection
I discovered that exceeding a hoist’s capacity can break parts and endanger workers. Overload protection is a game-changer.
Sensors or mechanical switches detect when the load surpasses safe limits. The hoist then stops lifting to avoid catastrophic failure.
I learned that some systems use load limiters or built-in torque sensors. They measure strain on the chain or rope. If a load feels heavier than safe, the device interrupts power. That prevents damage to motors, chains, and structures.
Benefits of Overload Protection
- Stops lifts when capacity is exceeded
- Minimizes mechanical stress
- Boosts operator confidence
Emergency Stop Buttons
I recall using an E-STOP once when a hook got snagged. That button’s immediate action avoided a big mess.
An E-STOP quickly halts power. It’s separate from standard controls, ensuring a reliable shutdown in emergencies.
I typically see bright red E-STOP buttons placed near the operator’s reach. They are designed to cut electricity instantly. That immediate response helps prevent accidents and reduces the risk of serious damage.
Key E-STOP Features
- Easily accessible location
- Bright, recognizable color
- Independent from regular controls
Safety Certifications
I used to check for brand reputations alone, but I learned official safety certifications matter most.
Look for OSHA and ASME compliance. That shows the hoist meets strict US regulations and testing standards.
I discovered that certifications validate design, construction, and performance. Hoists are often inspected at the factory and must follow guidelines for safe operation. Regular recertifications also keep equipment in top shape.
Recognized Certs and Standards
- OSHA (Occupational Safety and Health Administration)
- ASME (American Society of Mechanical Engineers)
- Verified inspection records
Additional Safety Features
- Braking Systems: Secure brakes keep loads suspended without slipping.
- Limit Switches: These cut power if the hoist tries to travel beyond set points.
- Control Systems: Smooth controls reduce load swings.
- Anti-Collision Systems: Prevent crashes in busy areas with multiple hoists.
What Are the Three Types of Chain Hoists?
I once faced a tricky lifting job. I only had a manual hoist, and it took forever. That experience showed me that different hoists fit different tasks and conditions.
The three main types of chain hoists are manual, electric, and pneumatic. Manual hoists need no power, electric hoists handle heavy loads swiftly, and pneumatic hoists excel in hazardous areas. Each type has specific pros and cons.
I remember watching a mechanic use a pneumatic hoist in a flammable environment. Seeing how it avoided sparks changed my perspective on hoist choices. Let’s look at each type’s features and best uses.
1. Manual Chain Hoists
I first encountered a manual chain hoist, also called a hand chain block. It’s straightforward to use but requires muscle power.
They rely solely on human effort. This design is affordable and portable. But it has limited capacity and can tire operators quickly.
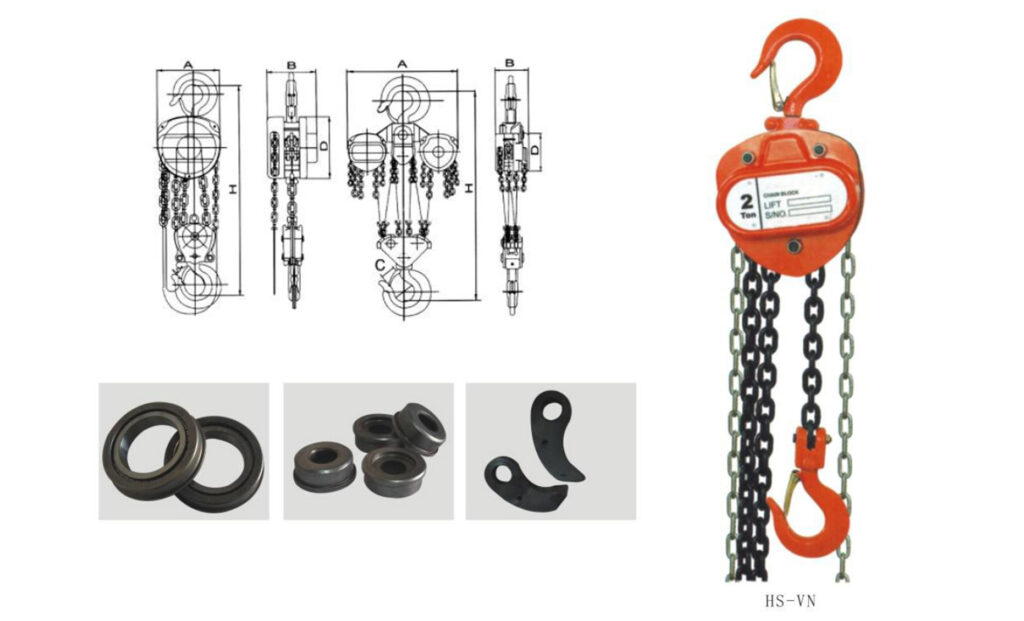
A typical manual hoist includes a chain loop you pull by hand. That action turns gears inside the hoist body, raising or lowering the load. It’s great for occasional, light lifting tasks or when you lack electricity. Yet, lifting speeds are slow, and the physical exertion limits productivity.
Key Advantages | Key Disadvantages |
---|---|
Portable, affordable | Labor-intensive |
Easy to operate | Lower lifting capacity |
No power needed | Slower lifting speed |
Best Use Cases: On construction sites without power or in maintenance tasks that need only occasional lifts.
2. Electric Chain Hoists
I saw an electric chain hoist in a busy warehouse. It zipped loads up and down efficiently, saving time and energy.
An electric motor handles the lift, allowing workers to manage heavier loads with less effort. That boosts productivity.
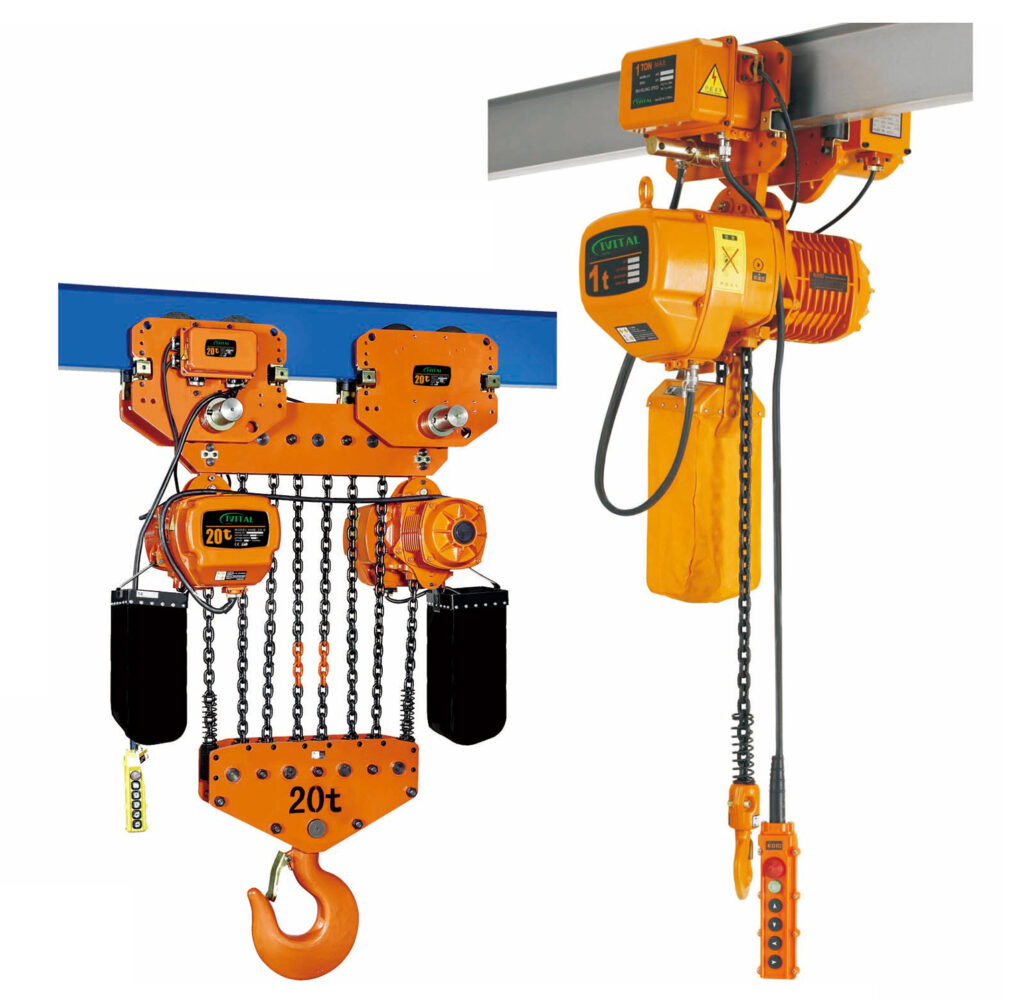
Electric chain hoists come in various capacities, often ranging from a few hundred pounds up to multiple tons. Many have variable speed controls for precise positioning. While the higher purchase cost and need for a power supply can be drawbacks, their ability to handle continuous heavy lifting usually justifies the investment.
Key Advantages | Key Disadvantages |
---|---|
High lifting capacity | More expensive than manual hoists |
Fast, efficient operation | Requires electrical power |
Reduced operator fatigue | Potential downtime if power fails |
Best Use Cases: Manufacturing plants, large warehouses, and construction projects with steady power access.
3. Pneumatic Chain Hoists
I once saw a pneumatic hoist in a chemical plant. The spark-free design kept everyone safe in a potentially explosive setting.
Powered by compressed air, these hoists are an excellent choice for hazardous or flammable environments. They can run continuously without overheating.
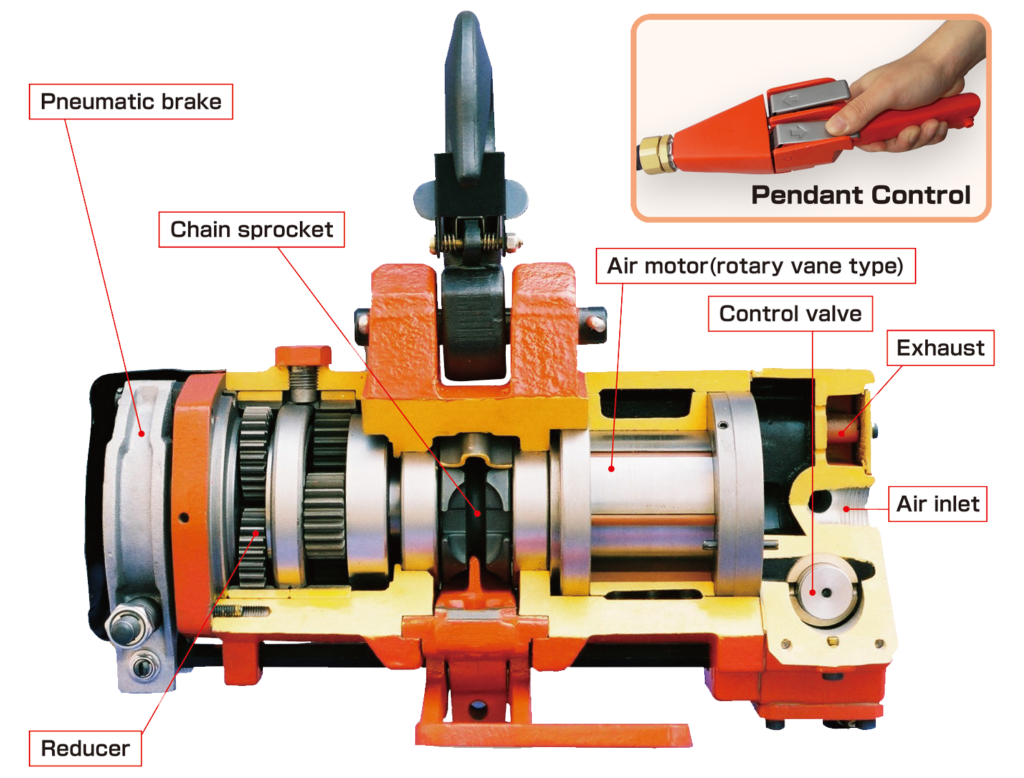
A pneumatic hoist converts compressed air into mechanical energy. This approach avoids the risk of electrical sparks. These hoists typically weigh less than their electric counterparts and handle heavy or frequent loads well. However, you must have a reliable compressed air supply, which can add infrastructure costs.
Key Advantages | Key Disadvantages |
---|---|
Safe in flammable conditions | Requires compressed air supply |
Continuous operation possible | Potentially higher maintenance |
Lightweight design | Noise from air-powered systems |
Best Use Cases: Oil refineries, chemical processing plants, or any facility requiring spark-free equipment.
How Does the Work Environment Influence Hoist Selection?
I once installed a hoist in a freezing warehouse and realized my standard model wasn’t suited for low temperatures. That made me see how different environments can shape hoist choices.
Work environments influence hoist material, design, and safety needs. Cold storage areas demand anti-corrosion coatings and cold-friendly lubricants. Hazardous areas require explosion-proof parts or spark-resistant materials. Failing to match hoist specs to the environment can cause breakdowns or accidents.
I recall the day I struggled with a hoist that froze in a sub-zero facility. That incident led me to research how specialized hoists handle extreme conditions. Let’s examine practical tips for two common setups: cold storage and hazardous zones.
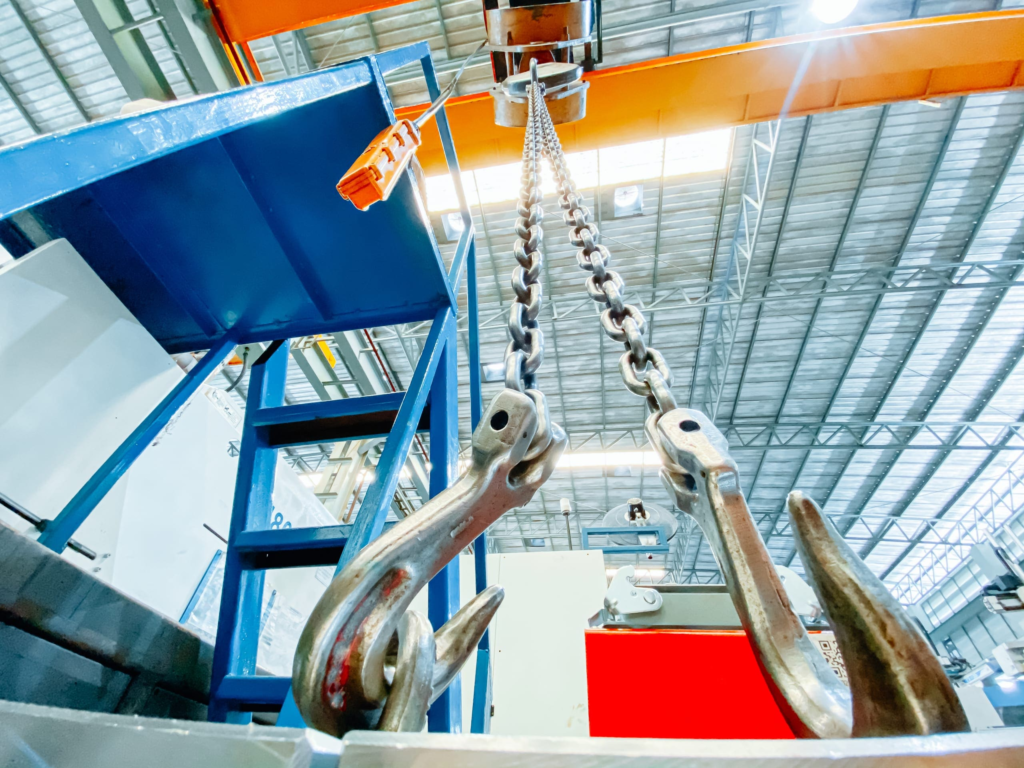
Choosing Hoists for Cold Storage Environments
I found that typical hoists may stiffen or corrode in cold storage. This section explains how to pick a model that can resist freezing temperatures.
Look for materials that keep their strength in sub-zero conditions. Compatible lubricants also matter, so standard oils don’t thicken. Insulated or sealed designs help minimize moisture-related wear.
I noticed that stainless steel often works well against corrosion in damp cold rooms. Coatings that lock out condensation can stop rust before it forms. Below is a quick view of factors I consider:
Material and Finish
- Stainless steel or specialty coatings
- Gaskets or seals to block moisture
Lubrication
- Low-temperature lubricants
- Regular checks to prevent thickening
Factor | Tip for Cold Storage |
---|---|
Material | Stainless steel or coated surfaces |
Lubricant | Low-temp grease or oil |
Design | Insulation or seal against moisture |
Choosing Hoists for Hazardous Areas
I once visited an oil refinery that demanded spark-free equipment. This section helps you pick a hoist safe for flammable or combustible atmospheres.
Select a hoist rated for the correct hazardous class. Look for explosion-proof enclosures, spark-resistant metals, and sealed electrical parts. Extra safety gear lowers the chance of igniting vapors or dust.
I learned that hoists for hazardous sites often have bronze hooks or ATEX certifications. Their motors are sealed to contain sparks. Maintenance schedules might also be stricter due to the harsh environment.
Environment Classification
- Check Class/Division (e.g., Class I, Div 1)
- Follow local regulations
Ignition-Resistant Components
- Spark-proof metal alloys
- Enclosed electrical designs
Factor | Tip for Hazardous Areas |
---|---|
Classification | Confirm correct Class/Div rating |
Spark Resistance | Bronze or stainless steel components |
Electrical Enclosure | Explosion-proof or fully sealed motors |
Summary
Choosing the right electric chain hoist can revolutionize your warehouse operations, ensuring safety and efficiency. By focusing on capacity, duty cycle, safety features, and brand reputation, you can make an investment that pays off in long-term reliability. Need help finding the perfect hoist? Let’s start the conversation.