I have worked with electric hoist systems in many heavy industry projects. Choosing the right control system has always been a challenge. Without proper features, the equipment could break down, or even worse, cause safety risks. So, I started looking for the key features that make a hoist system work efficiently. Let me share what I found.
An efficient electric hoist control system should include remote control capabilities, advanced safety features like overload protection, compatibility with existing lifting systems, and user-friendly interfaces. These elements maximize operational efficiency, ensure safety, and reduce downtime.
Let’s break down these features and explore why they are essential for heavy industry applications.
What Makes a Hoist Control System Efficient?
A smooth, efficient hoist control system boosts productivity, cuts energy costs, and enhances safety. Discover the key elements that make it perform at its best.
A reliable hoist control system blends proper load management, advanced control features, and consistent upkeep. By matching capacity accurately, using Variable Frequency Drives, and scheduling regular checks, you optimize performance, save energy, and reduce breakdowns.
Let’s explore the broader impacts of efficiency. An undersized hoist risks strain and faster wear, while an oversized one wastes energy and inflates costs. Striking the right balance requires careful capacity planning, data-driven performance monitoring, and thorough operator training. By integrating energy-saving components, like regenerative braking or smart controls, you further minimize operational costs. Regularly reviewing maintenance logs also helps you identify patterns, address small issues before they escalate, and extend your hoist’s overall lifespan. This holistic approach ensures every lift is precise, safe, and cost-effective for the long term.
How Does a Hoist Controller Work?
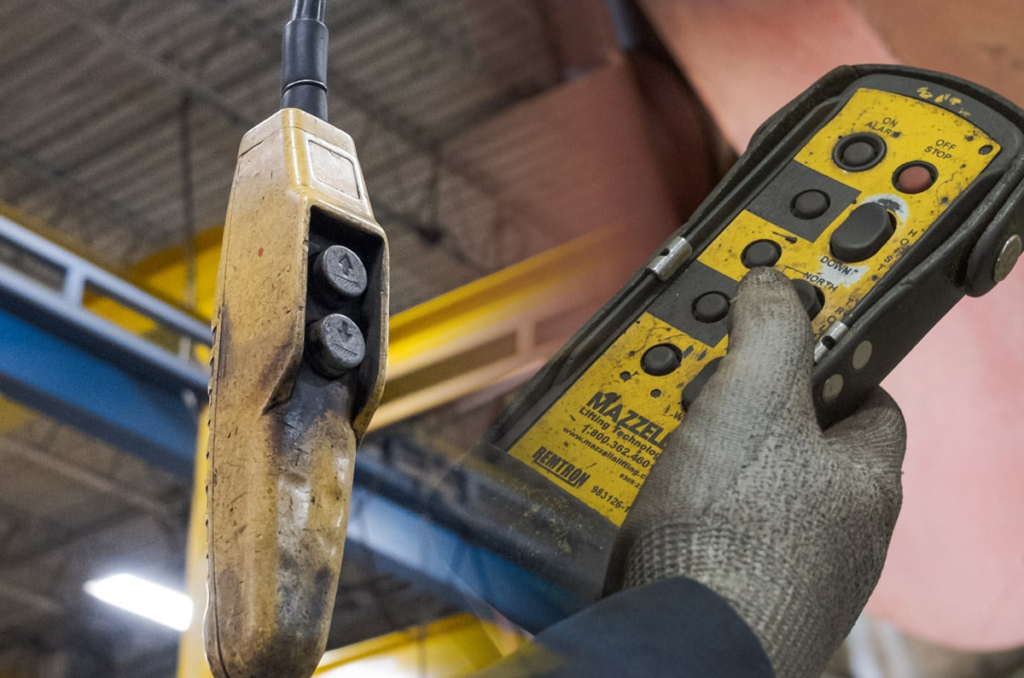
A hoist controller transforms simple commands into powerful lifting motions. It coordinates motors, brakes, and safety systems to move heavy loads smoothly and keep operations secure.
A hoist controller reads operator inputs, activates the motor, and transfers torque through gears. It uses limit switches and brakes to manage speed and stop positions, ensuring safe, accurate load handling.
When I explore hoist controllers, I see them as the brains behind modern lifting. The operator’s button press or joystick movement travels to an electric panel, which interprets those signals. It then powers the motor and releases the brake, turning electrical energy into mechanical force. Through gear reduction, the motor’s torque increases, letting the drum or chain handle substantial loads. But efficiency alone isn’t enough. Safety features, like limit switches, prevent the hoist from over-traveling, while an emergency stop button halts everything if something goes wrong. This multi-layered setup shows that hoist controllers balance raw power with precise oversight. By thoughtfully integrating brakes, overload protection, and real-time feedback, they ensure stable, controlled lifts for a wide range of industrial tasks.
Which Safety Features Are Essential in Electric Hoists?
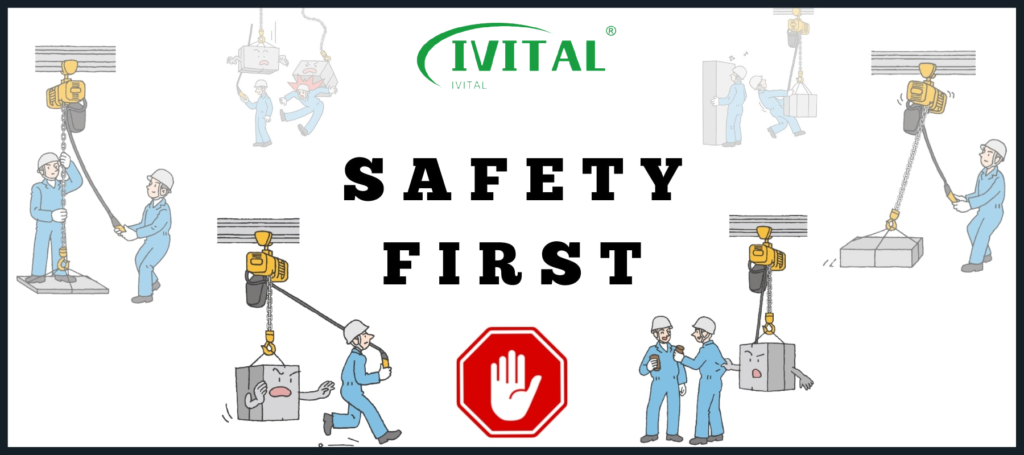
Electric hoists move heavy loads with precision, but reliable safety features protect both workers and equipment. Let’s see which components keep operations secure and prevent accidents.
Overload protection, emergency stops, limit switches, and robust brakes are the cornerstones of hoist safety. They halt dangerous motions, ensure proper load capacity, and keep everyone safe during lifting tasks.
When I explore electric hoist safety, I look for tools that go beyond mere compliance. Overload protection prevents operators from pushing equipment beyond its limits, which reduces system strain and costly repairs. Emergency stops let me shut down motion instantly if I notice a hazard. Limit switches stop the hook before it exceeds its travel range, preventing collisions with the hoist frame. Quality brakes hold loads securely during pauses, which eliminates the risk of uncontrolled drops.
But some hoist systems introduce extra layers of security. Anti-collision devices become vital in busy workplaces where multiple hoists operate. Thermal protection keeps the motor from overheating, ensuring consistent performance. Rope loosening limiters avoid dangerous slack by ensuring cables stay taut, so loads don’t swing wildly. Finally, maintenance alerts and inspection prompts help me stay on track with preventive care, highlighting potential issues before they become emergencies. By blending these features, modern hoists serve as reliable partners, lifting not only cargo but overall workplace safety.
Why Is Compatibility with Existing Equipment Important?
Achieving smooth operations often hinges on how well new tools integrate with your current setup. Compatibility preserves existing workflows and safeguards investments from costly disruptions.
Compatibility ensures seamless communication, avoids wasteful retrofitting, and lowers downtime risks. This synergy boosts productivity, fosters consistent performance, and curtails overhead, letting teams focus on growth rather than troubleshooting.
When organizations adopt new technology that aligns with their established systems, they save both time and resources. Compatibility minimizes the need for major overhauls, which lowers costs associated with retrofitting or replacing core equipment. It also keeps critical services running while new tools are phased in, helping teams stay productive. In data-rich environments, compatible devices communicate easily, sharing information without glitches or conflicting protocols. This harmony improves workflow coordination and reduces the likelihood of errors stemming from mismatched hardware or software. Compatibility also promotes future scalability: as the company expands, it can integrate upgraded devices without uprooting the entire infrastructure. By standardizing equipment and ensuring each component cooperates well, businesses foster smoother operations, greater reliability, and a strong platform for ongoing innovation.
What Are the Common Load Capacities for Electric Chain Hoists?
Electric chain hoists handle tasks from light workshop lifting to massive industrial loads. Let’s explore the typical capacity ranges that cater to various needs and industries.
Most electric chain hoists span capacities from 0.125 tons to over 50 tons. Smaller units cover everyday applications, while larger models tackle demanding heavy-duty tasks across manufacturing, construction, and specialized industrial settings.
When I look at electric chain hoists, I see a broad spectrum of lifting capabilities suited to different environments. Lighter-duty hoists, often rated between 0.125 tons (250 lbs) and 2 tons (4,000 lbs), handle tasks like workshop projects or small-scale material handling. Medium-duty hoists push capacities from 2 to 5 tons, which fits common factory and construction site needs. For heavier lifts—like large machinery or sizable building components—hoists ranging from 5 to 20 tons become essential. But some industries, such as shipbuilding or large-scale infrastructure projects, need specialized models that exceed 50 or even 100 tons. This versatility makes electric chain hoists a mainstay in diverse workplaces, ensuring that each load size meets a matching hoist capacity. By understanding these ranges, you can align your hoist choice with both immediate project demands and future scalability.
How Remote Control Enhances Hoist System Efficiency
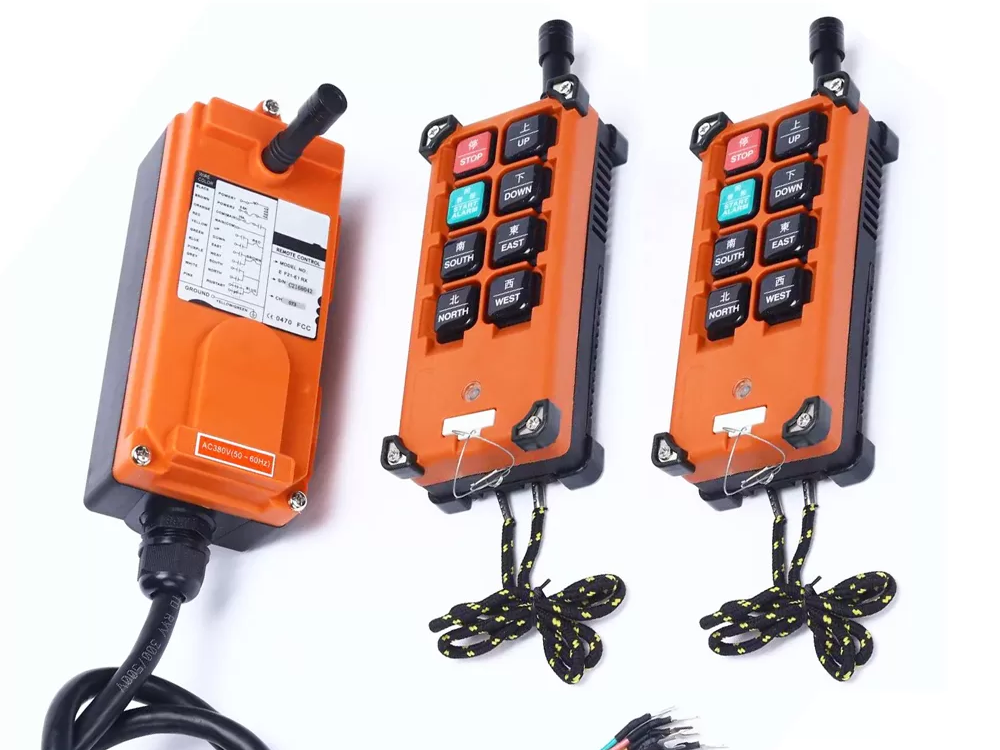
I’ve seen how remote controls give ecletric chain hoist freedom to move around, spot dangers sooner, and operate hoists with precision. They make every lift safer and more productive.
Remote controls boost efficiency by letting me position myself strategically, handle multiple hoists alone, and avoid direct exposure to moving loads. They cut operational time, reduce fatigue, and improve on-the-job safety.
When I use remote controls, I can stand exactly where I have the clearest view of both the load and surrounding hazards. This positioning cuts down on guesswork and helps me control lifts with confidence. I’ve also noticed that controlling multiple hoists from one device saves time, because I’m not shuffling between different pendants or relying on extra personnel. That mobility keeps me out of harm’s way, especially in busy or hazardous sites. Over time, I’ve seen fewer accidents because nobody has to stand near suspended loads or heavy machinery. These handheld devices are often designed with ergonomic features, which lessen arm strain and let me work for longer stretches without fatigue. Plus, some remote control models include data monitoring, so I can track load weights and run-time usage. This analytics feature makes predictive maintenance much easier. By integrating remote control systems into my hoisting operations, I increase productivity while reducing downtime, equipment damage, and safety incidents.
Conslusion
A robust electric hoist control system is the backbone of efficient material handling. By incorporating features like remote controls, safety mechanisms, and compatibility with existing equipment, you can enhance productivity and reduce downtime. Evaluate your needs, consult with suppliers, and invest in the best technology for your operations.