I never approve equipment without checking the load rating—and what’s behind it.
The Safe Working Load (SWL) depends on material strength, equipment design, usage method, and environmental conditions. Each factor directly influences how much weight your lifting gear can handle.
I once rejected a crane hook because a slight deformation changed its load capacity—and that decision probably avoided a failure.
[Table of contents]
- What factors influence the Safe Working Load of lifting gear?
- How does material strength affect load capacity?
- Why does sling angle or attachment point matter?
- Can design or connection method change the SWL?
- How do environmental conditions impact lifting limits?
- Conclusion
What factors influence the Safe Working Load of lifting gear?
Understanding SWL isn’t about guessing—it’s about knowing the inputs.
SWL is affected by material strength, wear condition, load angle, equipment design, and environmental stress.
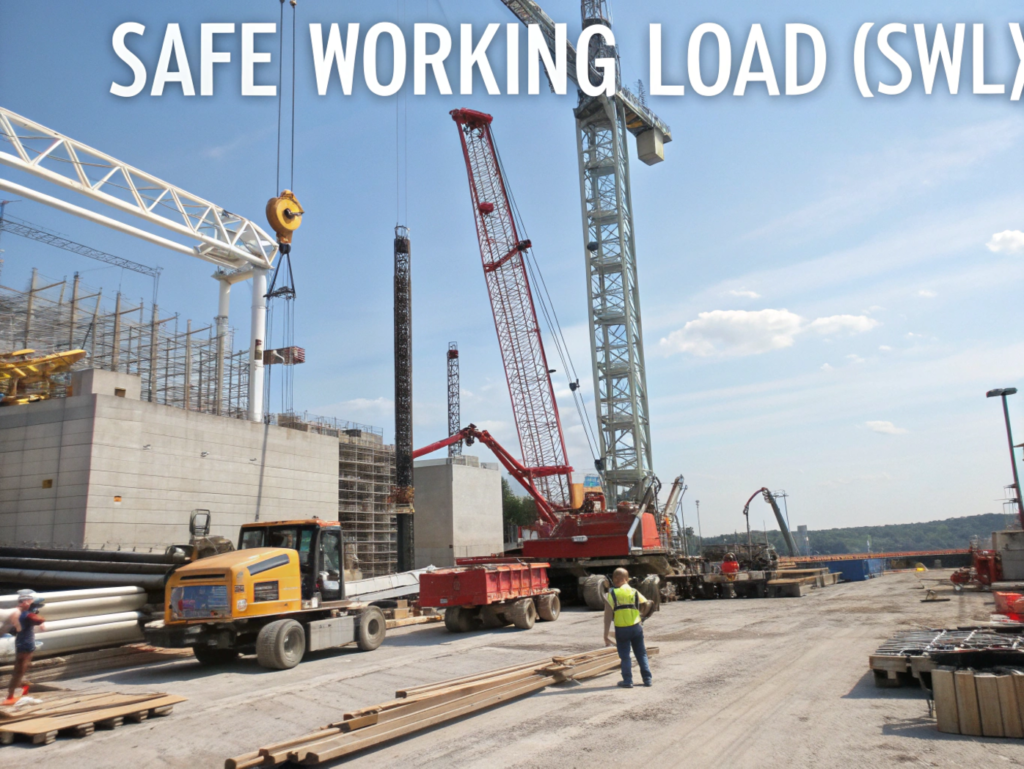
Dive Deeper
These are the core variables that manufacturers and engineers use to determine SWL:
Factor | Impact on SWL |
---|---|
Material strength | Directly sets maximum theoretical load |
Safety factor | Reduces max capacity for safety margin |
Sling angle | Alters force distribution and tension |
Connection type | Impacts load sharing or shift |
Wear and surface damage | Lowers effective load capacity |
No single factor is safe to overlook. All must be evaluated before use.
How does material strength affect load capacity?
You can’t cheat physics—stronger materials carry more.
Higher tensile strength and better metallurgy directly increase a product’s breaking point, which defines SWL.
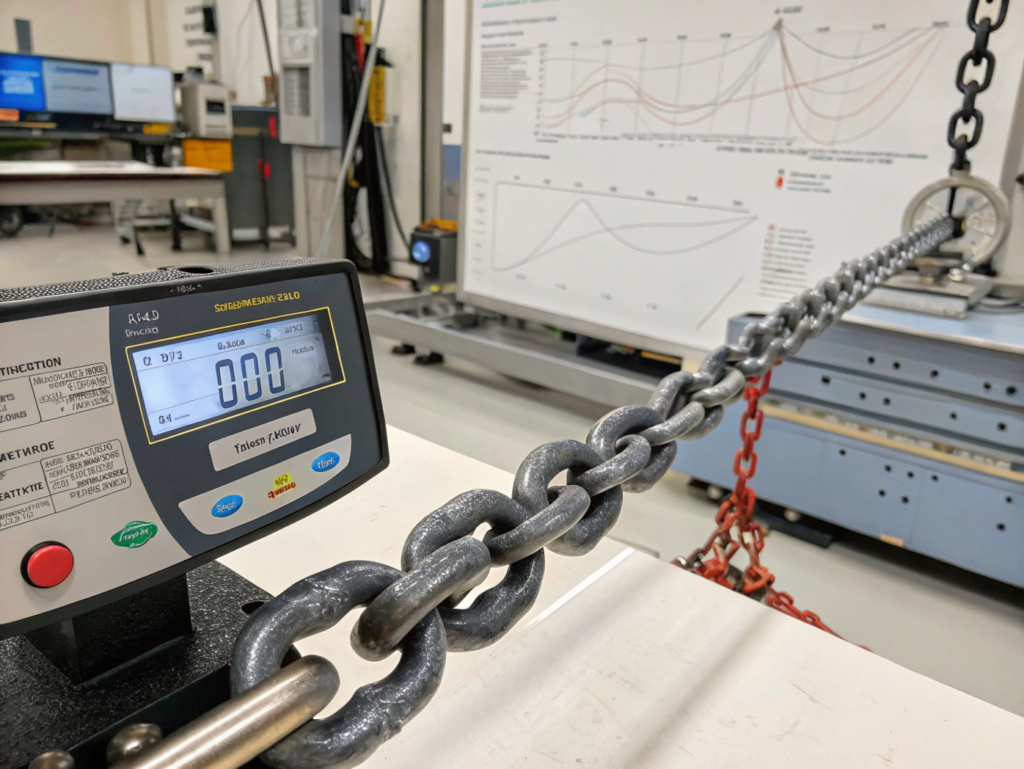
Dive Deeper
Steel grade matters. For example:
Chain Grade | Typical MBL (tons) | SWL (tons at 5:1 SF) |
---|---|---|
G70 | 3.5 | 0.7 |
G80 | 5.0 | 1.0 |
G100 | 6.3 | 1.26 |
But strength can degrade. Corrosion, fatigue cracks, or heat exposure all reduce true load-bearing ability—often invisibly.
Why does sling angle or attachment point matter?
Even perfect gear fails if the angles are wrong.
When a sling is not vertical, the load increases on each leg due to angle geometry.
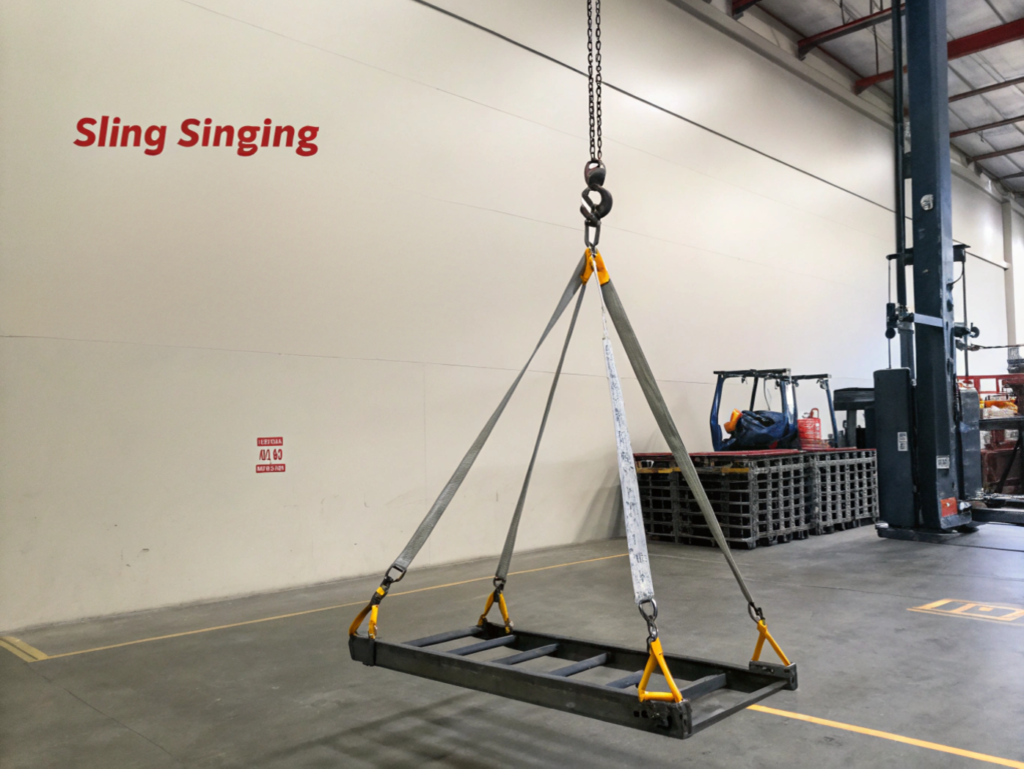
Dive Deeper
A vertical lift uses full capacity. But with angled slings, tension increases:
Sling Angle | Load Factor (per leg) |
---|---|
90° | 1.00 |
60° | 1.15 |
45° | 1.41 |
30° | 2.00 |
If you’re using a two-leg lift at 30°, each leg handles twice the weight. Many failures happen because the angle was ignored or misjudged.
Can design or connection method change the SWL?
Not all rigging is equal—even if it’s the same size.
The type of hitch or connection method significantly affects how loads are distributed and where stress builds up.
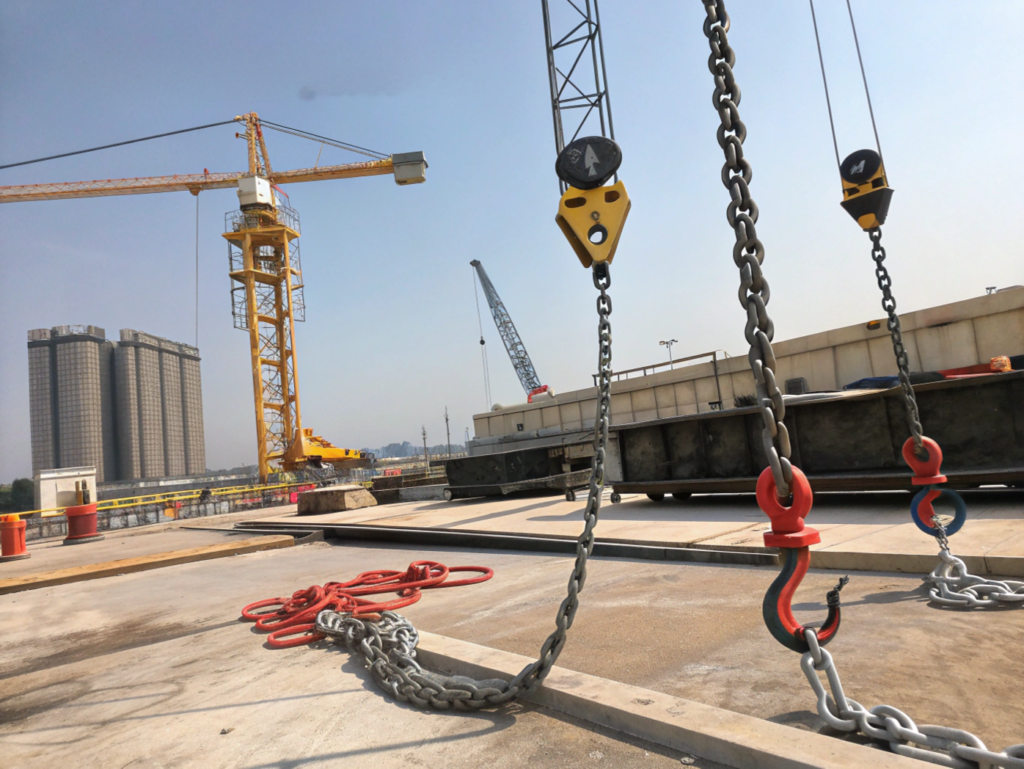
Dive Deeper
Let’s compare three common rigging setups:
Configuration | SWL Efficiency |
---|---|
Vertical Hitch | 100% of rated load |
Basket Hitch | 200% of SWL |
Choker Hitch | ~75–80% of SWL |
Also, consider if components are bolted, welded, or mechanically clamped. Stress concentrations in poorly designed joints often lead to failures below the theoretical SWL.
How do environmental conditions impact lifting limits?
It’s not just the lift—it’s where and how you lift.
Extreme temperatures, corrosion, moisture, and vibration can lower SWL even when gear appears fine.
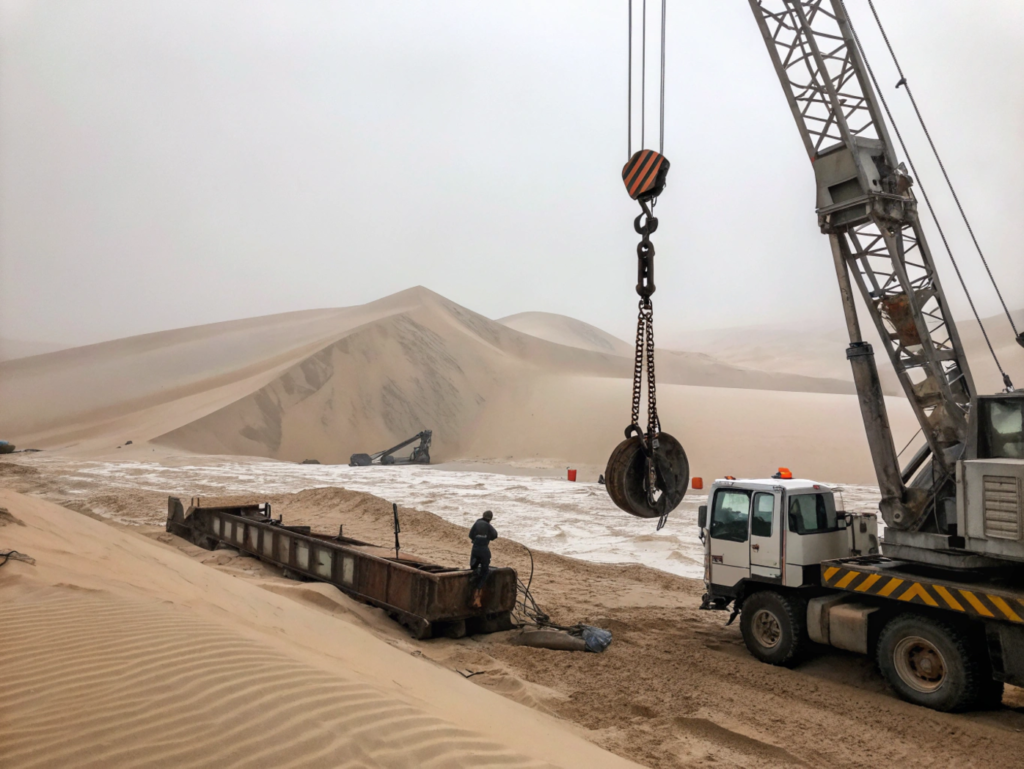
Dive Deeper
Situations I’ve seen firsthand:
- A chain sling rated for 2 tons failed at 1.5 tons after working months in a saltwater dock environment.
- Cold weather caused brittle fracture in a hoist hook that had no signs of damage.
Environment | Impact |
---|---|
Salt or moisture | Accelerates corrosion |
Heat (>200°C) | Weakens steel microstructure |
Cold (<0°C) | Increases brittleness |
Vibration/shock | Leads to fatigue or cracks |
If the job site is tough, the gear must be tougher—or SWL must be derated.
Conclusion
Safe Working Load is a system—not a sticker.