Selecting the right hoist control system—wired or wireless—can make a significant impact on your operations. With factors like mobility, safety, and site-specific needs in play, understanding their differences is critical for informed decision-making.
Wired hoist controls offer stable and interference-free operation, making them reliable for environments where precision is essential. Wireless hoist controls, on the other hand, enhance mobility and flexibility, ideal for large-scale or complex operations. Both systems have unique advantages tailored to specific operational needs.
Let’s dive deeper into how these systems differ and the benefits they offer for various applications.
What Is the Difference Between electric chain Hoist and electric wire rope Hoist?
Mechanism of Operation
Electric chain hoists use a chain as the lifting medium. The motor drives a gearbox and a sprocket that moves the chain. This system offers smooth control. It also suits tasks that need accurate lifting.
Electric wire rope hoists use a wire rope wrapped on a drum. The motor turns the drum to raise or lower the load. This setup is good for long lifts. It also works well when you need to lift heavier loads.
Load Capacity
Electric chain hoists can lift smaller loads. Their range usually starts at about 1/8 ton. Some models can lift a few tons. They are good for light tasks that need precise handling.
Electric wire rope hoists can lift larger loads. Some models handle 100 tons or more. They work well in heavy industries like construction or steel plants.
Size and Design
Electric chain hoists are compact. They fit in spaces with low headroom. They have a simple chain container that reduces bulk.
Electric wire rope hoists need more space. They have a drum that stores the rope. The larger structure can limit use in tight areas.
Applications
Electric chain hoists work well in assembly lines and warehouse environments. They help with smaller tasks that need fine positioning.
Electric wire rope hoists work well in places that require heavy lifting. They help in shipyards, building sites, and heavy factories.
diveDeeper
Overview of Core Features
Here is a simple table that shows some key points:
Feature | Chain Hoist | Wire Rope Hoist |
---|---|---|
Load Range | Up to a few tons | Often over 100 tons |
Size | Smaller | Bigger due to the drum |
Lift Precision | Very accurate | Good control, but some sway |
Maintenance Effort | Less complex | More complex and costly |
Common Use Cases | Lighter goods | Heavy projects |
Electric chain hoists often shine in smaller areas. The chain mechanism offers precise movement. The chain design works best for short or moderate distances.
Electric wire rope hoists often handle demanding tasks. They move large loads over greater distances. They also need a robust drum and wire rope.
Maintenance Tips
Maintenance is important. Users should check wear on chains, ropes, and gears. Users should also follow a set schedule for inspection.
Part to Check | Chain Hoist | Wire Rope Hoist |
---|---|---|
Chains / Ropes | Look for stretch or damage | Look for broken wires or kinks |
Gearbox | Check oil levels and wear | Check oil levels and wear |
Hooks and Latches | Inspect for cracks | Inspect for cracks |
Electrical Connections | Keep wiring secure | Keep wiring secure |
What is the main difference between a hoist and a crane?
The main difference between a hoist and a crane is in how they move loads. A hoist moves loads only up and down. A crane can move loads up, down, and sideways. This post will show how their functions and movements differ.
Hoist
A hoist lifts and lowers loads on a single plane. It attaches to a trolley on a beam. It gives some horizontal motion, but it does not move loads over a wide area.
Key Points
- Primary Use: Lifting and lowering in one vertical path.
- Movement: Up and down, with limited sideways motion.
- Common Tasks: Warehouse work or assembly lines with simple, vertical lifting needs.
Crane
A crane is a larger system. It includes a hoist plus extra parts like a trolley and a bridge. It can lift loads and move them in multiple directions.
Key Points
- Primary Use: Lifting, lowering, and moving loads across a wider area.
- Movement: Vertical and horizontal, covering bigger distances.
- Common Tasks: Large sites, such as construction areas or heavy manufacturing facilities.
diveDeeper
Comparison Table
Here is a simple table that shows their main differences:
Feature | Hoist | Crane |
---|---|---|
Primary Movement | Vertical (up and down) | Vertical and horizontal |
Complexity | Simple lifting device | Integrated system with multiple parts |
Typical Use | Smaller tasks in controlled spaces | Large-scale projects over wide areas |
Flexibility | Limited side-to-side movement | Can reach multiple points in a work zone |
When to Choose Each
Users pick a hoist when they only need to lift loads in one main spot. This works well for smaller tasks where space is tight. Users pick a crane when they must move heavy loads across different points in a facility. This is best for bigger tasks that call for more reach.
Final Thoughts
A hoist focuses on lifting loads vertically. A crane goes further and moves loads in different directions. A hoist is often part of a crane, which expands its range of motion. Each choice depends on the size of the task and the area of operation.
What is a radio-controlled crane?
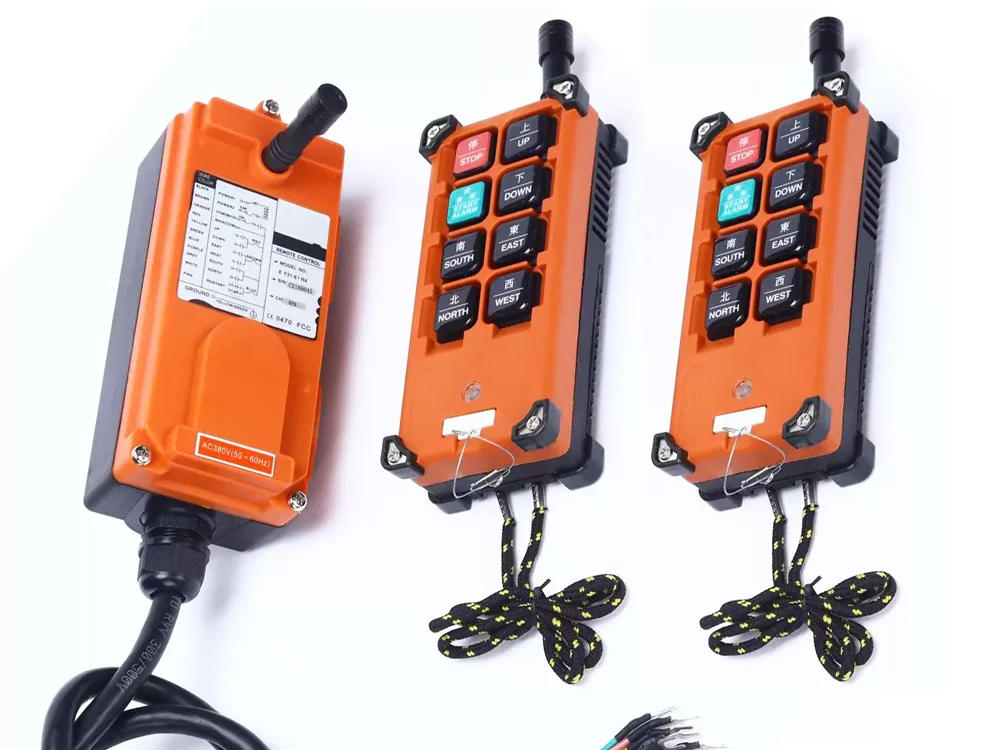
A radio-controlled crane is a lifting device that uses radio signals for remote operation. The operator carries a handheld transmitter. The crane has a receiver that reads these signals. This setup lets the operator stand away from the load. The operator sees the area more clearly and avoids dangerous spots.
Key Features
Remote Operation
The operator presses buttons on a small controller. The crane moves according to those signals. This method removes the need to stand close to the load.
Enhanced Safety
The operator keeps a safe distance from the load. The operator also sees the load path better. This lowers the risk of accidents.
Precision Control
Radio systems often give accurate control over crane motions. They help position loads in tight or crowded areas. This is helpful in places where precision is needed.
Versatile Uses
- Warehouses: Move and place items on racks.
- Construction: Lift building materials to specific spots.
- Manufacturing: Transfer parts across production lines.
- Maintenance: Handle overhead repairs without extra steps.
diveDeeper
Key Differences with Traditional Systems
Feature | Radio-Controlled Crane | Pendant-Controlled Crane |
---|---|---|
Operation Range | Extended range with no cables | Limited by cable length |
Safety | Operator stands far from load | Operator stands under the load |
Movement Flexibility | Operator can move around freely | Operator stays near control box |
Many facilities choose radio-controlled cranes. They want better safety and a clear line of sight.
Frequency and Signal Strength
Most radio-controlled cranes use common radio frequencies. They often include channels that can be changed if interference occurs. This design keeps the crane responsive.
Maintenance Tips
Part | What to Check | How Often |
---|---|---|
Transmitter | Battery level | Daily |
Receiver | Signal strength | Weekly |
Crane Motors | Unusual noise | Monthly |
Safety Latch | Wear and tear | Monthly |
Operators should replace batteries when they get low. They should also keep the transmitter clean. This will help prevent stuck buttons.
Advantages Over Traditional Controls
- Freedom of Movement
The operator can walk to a better vantage point. This makes it easier to guide loads. - Better Productivity
One operator may control more than one crane if needed. This can save labor. - Less Signal Interference
Modern radio systems are stable. They face fewer signal issues than older remote setups.
Wired vs. Wireless Hoist Systems: Key Comparisons
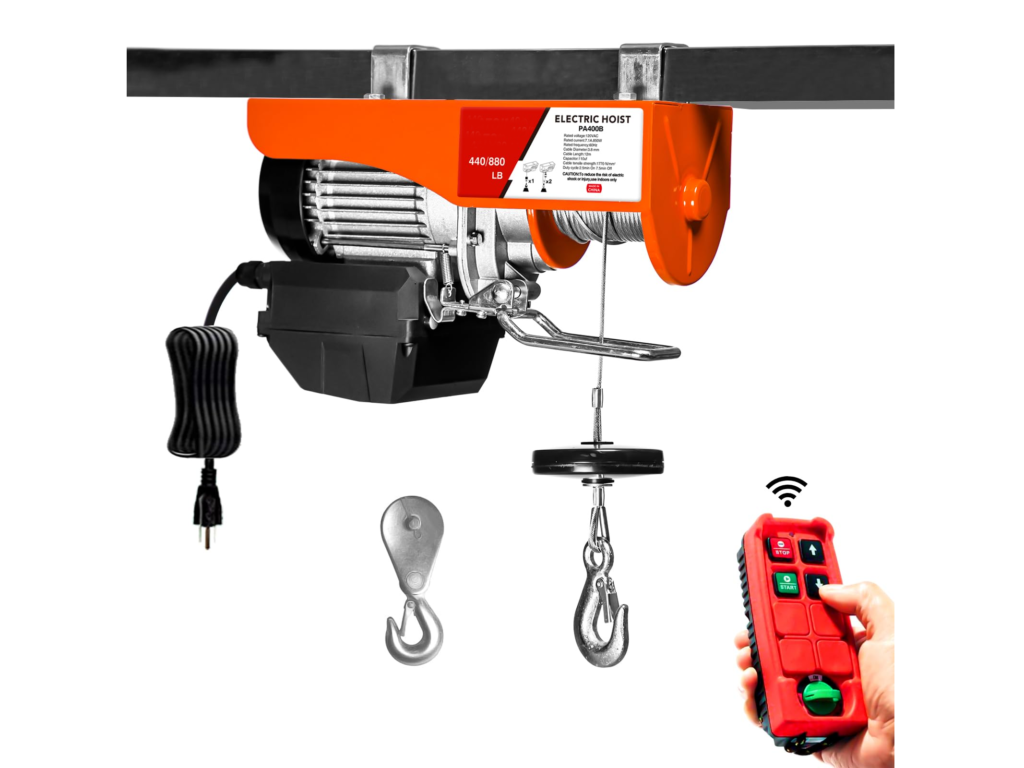
A hoist system can use wired or wireless technology. Each choice offers specific benefits and drawbacks. People often compare cost, reliability, safety, and maintenance needs.
diveDeeper
Cost and Installation
Wired hoist systems often cost more to install. They need cables, conduit, and sometimes large equipment for setup. One example involved about 1,000 feet of conduit, which led to high total costs. Wireless systems tend to cost less to install. They do not need as many cables or conduits. Some projects show significant savings when switching to wireless options.
Factor | Wired System | Wireless System |
---|---|---|
Cabling Needs | Extensive cabling and conduits | Minimal cabling, mostly power supply |
Installation Complexity | May need extra equipment | Often simpler to set up |
Typical Cost Range | Higher due to cable routing | Lower due to fewer hardware needs |
Reliability and Stability
Wired connections have a stable signal. They are not easily affected by outside noise or other signals. Many industrial sites trust wired systems for crucial tasks. Wireless connections offer more freedom but can face interference. Some environments have radio signals or physical barriers that may disrupt communication. Newer wireless systems use better technologies that reduce signal problems.
Safety and Operator Flexibility
Wired systems tether the operator to a fixed control panel. This can limit the operator’s view of the load or work area. Wireless systems let operators walk around. They can find a better vantage point for guiding loads. They can also keep a safer distance from potential hazards.
Feature | Wired System | Wireless System |
---|---|---|
Operator Mobility | Tied to the control panel | Can move to any safe spot |
Visibility of Load / Work Area | May be obstructed | Usually better |
Danger Zone Proximity | Closer to load | Often farther away |
Maintenance and Longevity
Wired systems can need repairs if cables become damaged. Yet they often have fewer electronic parts that need upkeep. Wireless systems have no main cable to break. They do need periodic checks to ensure remote batteries and signals work as they should. This difference can matter in harsh work settings.
Conclusion
Choosing between wired and wireless hoist controls depends on your operational priorities. Wired systems excel in reliability and interference-free performance, making them suitable for high-precision tasks. Wireless systems offer unmatched flexibility and modern capabilities, ensuring efficiency in large-scale or complex projects. Evaluate your site conditions and operational goals to select the system that aligns best with your needs.