Maintaining a 2-ton electric chain hoist is critical to ensure its longevity, efficiency, and safe operation. Whether you’re managing a warehouse or a construction site, implementing a consistent maintenance routine is key. In this article, I’ll cover essential tips, from daily inspections to troubleshooting common issues, that will help you keep your hoist in top shape while minimizing costly repairs.
Regular maintenance of your 2-ton electric chain hoist is essential for extending its lifespan and preventing breakdowns. Start with daily checks, including inspecting the chain for wear, ensuring proper lubrication, and cleaning debris from critical parts. Make sure electrical components are functioning properly and test the brakes and limit switches. Proper maintenance reduces the likelihood of costly repairs and improves safety by preventing accidents.
Now that we’ve covered the daily checks, let’s dive into more detailed aspects of hoist maintenance, such as troubleshooting common issues and safety checks to ensure peak performance.
How Do You Maintain an Electric Chain Hoist?
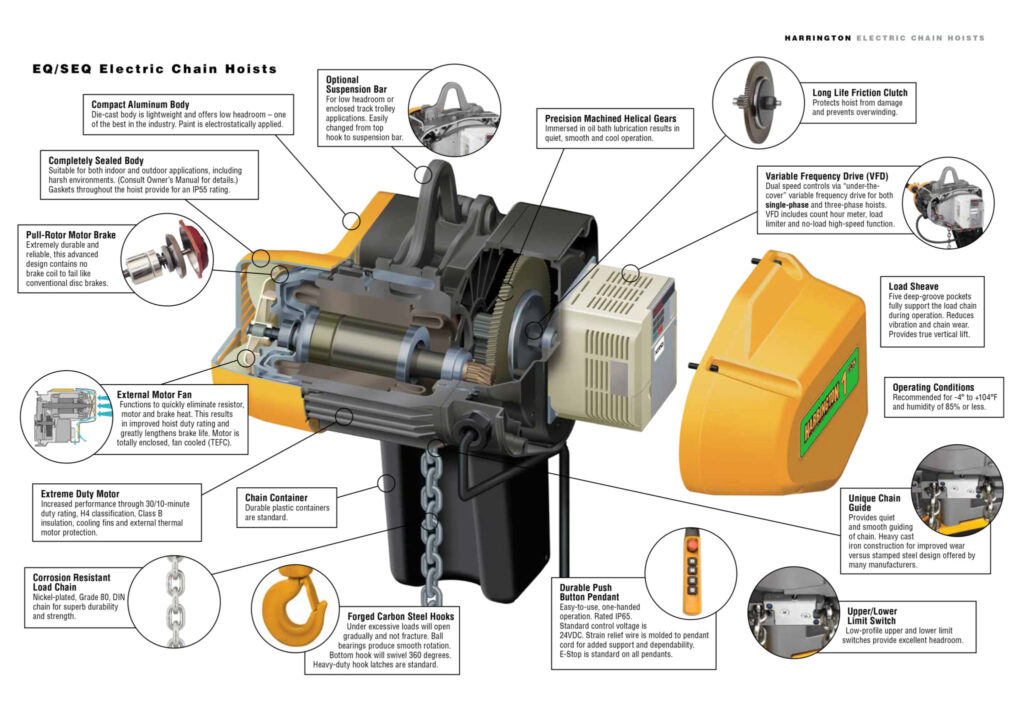
Regular maintenance is essential for ensuring the long-term reliability and safety of your electric chain hoist. By following a few simple practices, you can keep your hoist running smoothly and avoid costly downtime.
To maintain an electric chain hoist, perform daily visual inspections, clean the hoist regularly, lubricate moving parts, and check electrical components. These steps prevent premature wear and ensure smooth, safe operation.
Maintaining an electric chain hoist involves more than just performing basic tasks. For long-term reliability, you should carry out both daily and periodic checks.
- Daily Inspections: Start each day by visually inspecting the hoist, focusing on the chain, hooks, and motor. Ensure the chain isn’t worn or stretched excessively, as this can affect lifting capacity and safety. Check the hooks for cracks or deformation, which can lead to load detachment and accidents. Ensure the hoist’s motor is running smoothly, with no unusual noises or signs of overheating.
- Cleaning: Regular cleaning prevents the buildup of dirt, dust, and grime, which can impact the performance of the hoist. Use a dry cloth or brush to remove dust and debris from the motor, chain, and other exposed components. Avoid using excessive water during cleaning to prevent rust or internal damage. For deeper cleaning, use specialized cleaning agents, but be sure to dry everything thoroughly afterward.
- Lubrication: Apply appropriate lubricating oil or grease to key moving components like gears, bearings, and the chain. Lubrication reduces friction, prevents wear, and ensures smooth operation. Be cautious not to over-lubricate, as excess oil can attract dirt, leading to potential blockages or mechanical failures.
- Electrical Check: A vital part of hoist maintenance is inspecting electrical components such as the power supply, control systems, and circuit breakers. Ensure the connections are secure and free from corrosion. Regularly check for any signs of wear on cables or connectors. If any part of the electrical system is compromised, it could lead to power failure or even electrical hazards during operation.
By following these daily maintenance practices, you can extend the life of your hoist, prevent breakdowns, and ensure safe operation. Additionally, remember that weekly and monthly checks—such as testing the safety devices and conducting detailed inspections—are crucial for keeping the hoist in optimal condition.
How to Service a Hoist?
Servicing your electric chain hoist properly is essential for keeping it reliable and safe. Regular maintenance not only ensures optimal performance but can also prevent costly breakdowns.
To service your electric chain hoist, perform daily checks for damage, lubricate moving parts, and ensure proper function. A full inspection should be done annually, including load testing and professional servicing.
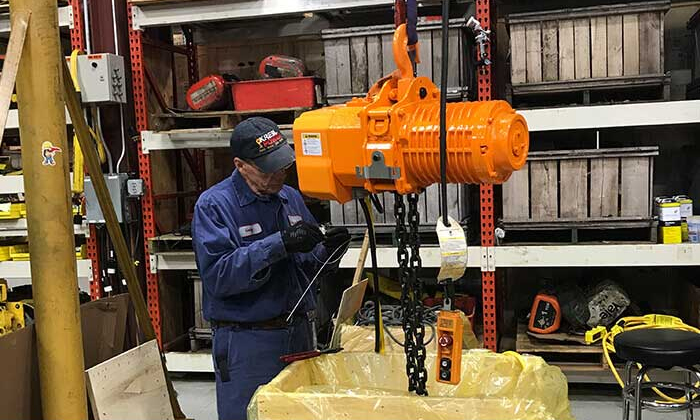
Effective servicing of an electric chain hoist is crucial to maintain its performance and longevity. Regular inspections and routine maintenance tasks should be conducted, starting with daily checks. Inspect the load chain, hooks, and electrical components for wear, rust, or damage. This ensures any potential issues are identified early. Weekly maintenance should include lubrication of the load chain and moving parts to reduce friction and avoid unnecessary wear. Inspect the electrical system for corrosion or damage to the wiring.
Monthly, conduct a more thorough examination of critical components like the brakes, limit switches, and control systems. Check that safety devices are operational, and assess the condition of the load chain, looking for elongation or pitting. If necessary, replace the chain to prevent failure during operation.
Once a year, schedule a professional inspection where the hoist undergoes load testing and an in-depth examination of both mechanical and electrical components. This step is vital for ensuring the hoist can safely handle its rated capacity and perform optimally. If the hoist has been involved in an incident, or if unusual noises or irregular performance are noticed, immediate servicing should be arranged.
By following these steps, including proper lubrication, load testing, and professional inspections, you can ensure that your hoist remains in peak condition, extending its lifespan and enhancing safety in your workplace.
What Are Common Problems and How Do You Troubleshoot a Hoist?
Electric chain hoists are designed to be reliable, but issues can arise during operation. Knowing the common problems and how to troubleshoot them can save you time, money, and stress. Let’s take a closer look at some frequent issues and their solutions.
Common problems with electric chain hoists include power supply issues, chain slippage, motor malfunctions, and brake failures. Troubleshooting these problems involves checking electrical components, ensuring proper lubrication, and inspecting mechanical parts for wear. By addressing these issues early, you can prevent costly repairs and downtime.
Electric chain hoists are essential for many industries, but like any mechanical system, they require maintenance and care. Below are some common issues you might encounter with your hoist, along with troubleshooting tips to get your hoist back in working order quickly and safely.
1. Hoist Does Not Operate
- Possible Causes: Incorrect power supply connection, blown fuse, or tripped circuit breaker.
- Solutions:
- Check the power supply to ensure it meets the hoist’s voltage requirements.
- Use a multimeter to verify that the voltage levels are correct.
- Inspect fuses and reset any tripped circuit breakers.
- Examine the control circuit and wiring for any damaged connections.
2. Motor Makes Noise but Does Not Rotate
- Possible Causes: Incorrect motor phase connection or mechanical blockage.
- Solutions:
- Verify that the motor’s electrical connections are correct. If necessary, swap the phase connections.
- Look for physical obstructions that might be preventing the motor from turning. If the load is too heavy, reduce the weight to avoid overload.
3. Chain or Wire Rope Cannot Be Raised or Lowered
- Possible Causes: Faulty stroke limiter or brake malfunction.
- Solutions:
- Inspect the stroke limiter for issues and replace it if needed.
- Check the brake mechanism for wear or failure. If necessary, adjust or replace the brake components.
4. Hoist Stops Mid-Lift
- Possible Causes: Voltage supply issues or phase loss in three-phase systems.
- Solutions:
- Measure the voltage at the hoist to ensure it’s within 10% of the rated voltage.
- If phase loss is detected, inspect the wiring and connections in three-phase systems.
5. Brake Failure
- Possible Causes: Worn brake pads or faulty brake mechanism.
- Solutions:
- Inspect the brake pads for wear and replace them as necessary.
- Ensure the brake mechanism is functioning properly, and adjust it if needed to maintain efficiency.
6. Control Failure (Hoist Does Not Respond to Controls)
- Possible Causes: Damaged control circuit or faulty controller.
- Solutions:
- Check all control circuit connections for integrity and repair any damaged wires.
- Inspect the controller for faults. Replace it if necessary.
7. Chain Breakage
- Possible Causes: Overloading, excessive wear, or poor operating conditions.
- Solutions:
- Immediately stop operation if the chain breaks.
- Assess load conditions and the environment before replacing the chain. Ensure proper installation of the new chain.
General Troubleshooting Steps:
- Check Power Supply: Always verify the hoist is receiving adequate power.
- Inspect Components: Look for visible wear, damage, or loose connections.
- Test Controls & Safety Features: Ensure that all controls, including emergency stops and limit switches, are working correctly.
- Consult Manufacturer’s Manual: For specific troubleshooting related to your hoist model, refer to the user manual.
- Seek Professional Help: If problems persist, contact a technician for a comprehensive inspection and repair.
By following these troubleshooting steps, you’ll be able to address the most common issues with your electric chain hoist, ensuring that it operates smoothly and safely.
Why are safety checks vital for electric chain hoists?
Electric chain hoists lift heavy loads and operate under intense pressure, making regular safety checks crucial. Neglecting these checks can lead to equipment failure, accidents, and even injuries. Let’s explore why these checks are so important.
Safety checks for electric chain hoists are essential to prevent accidents, maintain equipment integrity, comply with legal standards, and extend hoist lifespan. Regular inspections help detect issues early, ensuring safe and efficient hoist operation.
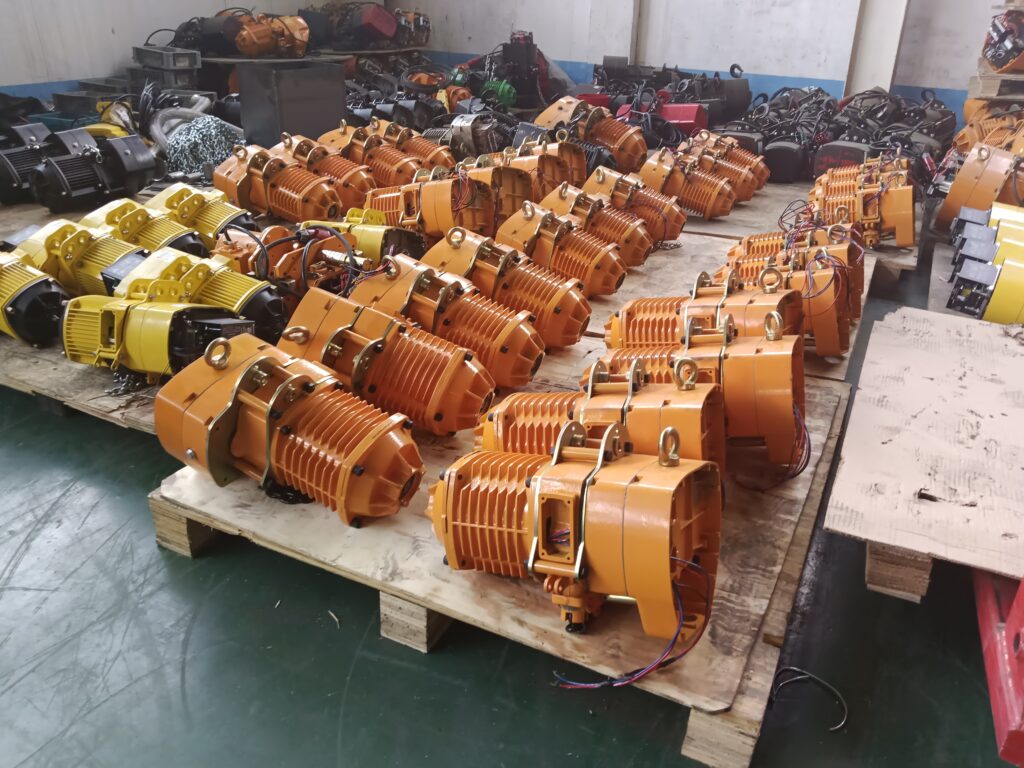
Safety checks are not just a formality; they are a critical component of maintaining a safe and efficient working environment. Electric chain hoists are responsible for lifting heavy loads, and any failure can lead to severe accidents, including the risk of dropped loads, injuries, or even fatalities. Regular safety inspections are crucial in identifying potential risks such as worn-out chains, malfunctioning brakes, or loose electrical connections before they cause operational failure. For instance, a damaged load chain could snap under pressure, causing the load to drop, resulting in serious injuries. Similarly, compromised brake systems can fail to stop the hoist in time, leading to accidents.
Neglecting safety checks not only jeopardizes employee safety but can also result in expensive equipment repairs, unplanned downtime, and legal penalties. In many jurisdictions, failing to conduct regular safety inspections can lead to fines or even workplace shutdowns due to non-compliance with safety regulations. These regulations ensure that hoists are operating at peak performance and reduce the risk of workplace injuries.
Additionally, regular safety checks contribute to operational efficiency. By ensuring that every part of the hoist, from the electrical components to the chains and hooks, is in good condition, workers experience fewer disruptions in their workflow. Preventing breakdowns helps maintain a smooth operation, reduces maintenance costs, and extends the lifespan of the hoist.
Ultimately, safety checks aren’t just about compliance—they’re about fostering a culture of safety within the workplace. Regular maintenance checks ensure workers are familiar with hoist safety features, reducing the likelihood of improper usage and enhancing awareness about the importance of safe lifting practices.
How to Extend the Lifespan of Your 2-Ton Electric Chain Hoist?
Proper care and routine maintenance are essential for prolonging the lifespan of your 2-ton electric chain hoist. Here’s how you can implement a maintenance plan that ensures smooth operation for years.
To extend the lifespan of your hoist, ensure regular inspections, proper lubrication, and cleaning. Prevent overloading, maintain the electrical system, and store it in optimal conditions to avoid corrosion and damage.
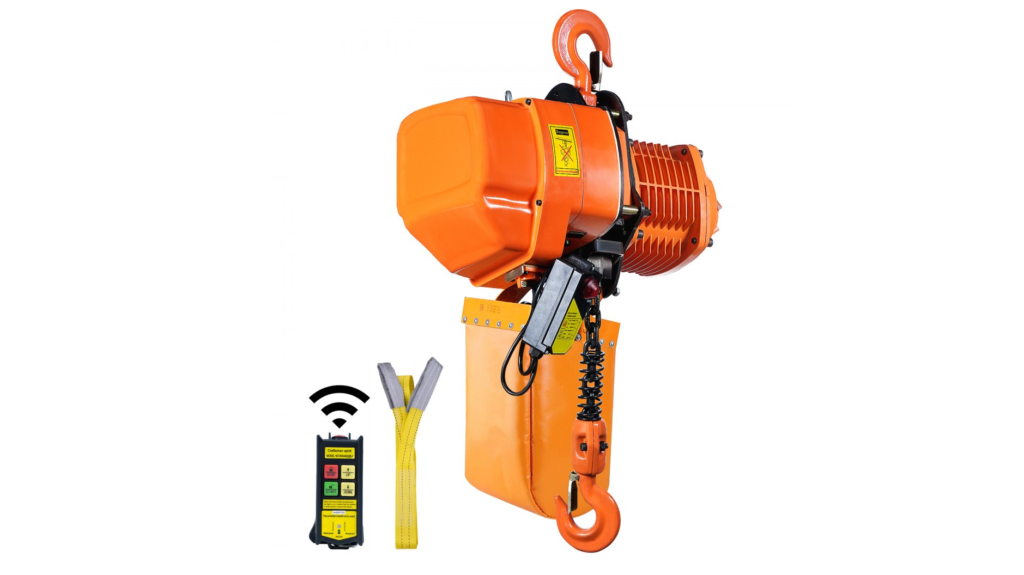
Extending the lifespan of your 2-ton electric chain hoist goes beyond just cleaning and lubrication; it requires a structured maintenance schedule. Regular inspections should be performed before and after each use. Start by checking the load chain for elongation or wear, inspect the hooks for any signs of deformation, and ensure that all safety mechanisms, such as limit switches, are functioning. Over time, even minor wear and tear can become serious issues if left unnoticed. Furthermore, always lubricate the load chain with a manufacturer-approved lubricant to reduce friction and prevent premature wear. Cleaning is equally important: dirt and debris can accumulate and wear out parts faster, so make sure to clean the hoist after each use.
The electrical system also requires attention. Routinely check the wiring, connectors, and switches for wear and damage. Ensure that all connections are tight and corrosion-free. Don’t forget to test the safety features, like limit switches and emergency stop buttons, to ensure they’re working properly. Storing the hoist in a dry, protected area is crucial to preventing rust and corrosion. Finally, avoid overloading the hoist; adhering to the specified load capacity is one of the best ways to prevent mechanical failure and extend its operational life. By following these steps, you ensure that your hoist runs efficiently and safely for a long time, avoiding costly repairs and downtime.
What Are the Signs Your Hoist Needs Repair?
Noticing when your 2-ton electric chain hoist needs repair is essential to avoid costly downtime and ensure safe operations. Let’s explore the common warning signs that your hoist requires attention.
Signs that your hoist needs repair include unusual noises, load drift, worn chains, weak brakes, electrical problems, and motor overheating. Regularly monitoring these issues will help you identify problems before they lead to major failures.
Understanding the signs of hoist damage is crucial for safety and efficiency in your operations. Let’s dive into the specifics of each sign:
1. Unusual Noises
Grinding or Clicking Sounds: If your hoist produces grinding, clicking, or other strange noises during operation, this is a clear indication that something is wrong. Such sounds often signal worn-out motor components, misaligned gears, or chain damage. These issues can cause significant performance degradation and should be addressed immediately to prevent further damage.
For example, grinding noises might come from an overworked motor or insufficient lubrication on the gears, while clicking sounds may be caused by debris caught in the chain. These small problems can quickly escalate if not handled promptly, making it crucial to inspect your hoist if you hear any unusual noises.
2. Load Drift or Creep
Inability to Hold Load: If your hoist struggles to hold a load in place when the lifting operation is paused, it could point to a problem with the braking system or limit switches. A hoist that cannot securely hold a load poses a significant safety hazard. This malfunction could be due to worn-out brake components or issues with the hoist’s electrical system.
If you observe any load drift or creep, it’s important to stop using the hoist immediately and have the braking system inspected and repaired by a professional. Ignoring this could result in a dropped load, potentially leading to damage, injury, or even fatalities.
3. Chain Issues
Worn or Elongated Chain: Over time, the chain in your electric hoist will naturally experience wear, but excessive elongation, rust, or cracks are signs that it’s time for a replacement. A weakened chain increases the risk of failure during lifting operations and may cause the load to fall unexpectedly. Always inspect the load chain regularly to ensure it’s in good condition, and replace it if you notice any wear or damage.
Remember, a compromised chain is a safety risk that can affect the performance of your hoist. If the chain is not functioning properly, it’s crucial to replace it before the hoist is used again.
4. Weak Brakes
Failure to Stop Load: The braking system is one of the most vital safety features of a hoist. If the hoist fails to stop the load securely or if the load drifts when the controls are released, there is likely an issue with the brakes. Weak or malfunctioning brakes not only affect hoist performance but also pose a serious safety risk, as they may fail to secure the load in place during operation.
To avoid this, ensure that the brakes are regularly inspected for wear and function. In some cases, cleaning or lubrication may restore functionality, but if the problem persists, a professional repair or replacement is required.
5. Electrical Problems
Damaged Electrical Components: The electrical system in your electric chain hoist can be susceptible to damage, especially in harsh working environments. Frayed wires, loose connections, or signs of overheating can lead to operational failures, and should be inspected regularly. Electrical faults can disrupt power flow, causing the hoist to malfunction or even stop working entirely.
Look out for any visible damage to the cables or components, and check for any signs of overheating in the electrical connections. If any of these issues are detected, the electrical system should be repaired immediately to avoid operational hazards.
6. Control Malfunctions
Unresponsive Controls: A hoist with unresponsive or delayed control buttons may be suffering from issues in the control circuit or wiring. If you notice that the hoist doesn’t respond immediately when you press the button or if there’s a lag between input and operation, this is a sign that the wiring or controls may be faulty.
Control problems can lead to erratic hoist behavior, which increases the risk of accidents. Ensure that your hoist’s controls are properly maintained and repaired if they start malfunctioning.
7. Motor Overheating
Excessive Heat During Operation: If the motor of your electric hoist becomes excessively hot during use, this could indicate overload conditions or internal mechanical issues. Overheating can damage the motor, decrease efficiency, and increase the risk of a fire. In many cases, overheating is caused by an overworked hoist, improper lubrication, or mechanical issues within the motor itself.
If you notice that the motor is overheating, immediately stop using the hoist, allow the motor to cool down, and investigate the cause. Continued overheating can lead to motor failure, which may require costly repairs or replacements.
8. Frequent Tripping of Circuit Breakers
Electrical Overload: Circuit breakers tripping frequently during hoist operation often signal an electrical fault or overload within the hoist. This could be due to a short circuit, damaged wiring, or an overloaded hoist. If circuit breakers continue to trip, it’s essential to examine the hoist’s electrical system to identify and resolve the issue.
Summary:
Maintaining your 2-ton electric chain hoist doesn’t have to be complicated. By following these maintenance tips and performing regular inspections, you can ensure the hoist’s longevity, prevent breakdowns, and keep your operations running smoothly. Remember, a little proactive maintenance goes a long way in minimizing downtime and repair costs.