What should I consider when choosing the right electric hoist control system?
In construction, manufacturing, and logistics, operational efficiency and safety hinge on having the right equipment. Selecting the perfect electric hoist control system ensures smoother lifting operations, minimizes downtime, and enhances workplace safety.
Key factors include load capacity, lifting height, control type (pendant or wireless), safety features (overload protection, limit switches), and compatibility with your facility’s power supply and duty cycle.
Now, let’s explore these considerations in detail to guide you in making the right choice.
What Factors Should Be Considered When Choosing a Hoist?
When selecting a hoist control system, these factors are crucial:
- Load Capacity: Determine the heaviest load you’ll be lifting and select a system that exceeds this weight.
- Lifting Speed: Faster speeds improve efficiency but must align with operational safety.
- Power Supply: Assess your facility’s power source to ensure compatibility.
- Duty Cycle: Choose a hoist that can handle the frequency and duration of use without overheating.
- Safety Features: Look for emergency stop options, overload protection, and smooth control mechanisms.
What Is the Best Type of Electric Hoist?
Choosing the right electric hoist can transform your lifting operations, ensuring efficiency and safety. A mismatch, however, could disrupt workflows and escalate risks. So, how do you make the best choice?
The best type of electric hoist depends on your needs. Lightweight hoists (440 lbs) suit smaller tasks, while heavy-duty options (6,600 lbs) excel in demanding environments. Consider control type, lifting height, and safety features like overload protection.
Imagine a construction site struggling with a hoist that’s too weak or unsafe. The result? Delays, accidents, and wasted resources.
What Is the Function of an Electric Hoist?
Electric hoists revolutionize lifting operations, providing efficient, safe, and versatile solutions for heavy or awkward loads. But what makes them indispensable tools across industries like construction and logistics?
Electric hoists lift, lower, and move heavy objects with precision. They reduce physical strain, enhance efficiency, and come equipped with safety features like overload protection and emergency stops to prevent accidents.
Picture a single worker safely lifting a load that previously required an entire team. That’s the transformative power of electric hoists
How I Choose the Right Hoist Capacity
When I need to pick a hoist, I always start by checking the weight I plan to lift. This includes everything—the load and any extra equipment or tools attached to it.
Finding the Right Capacity
If the load is between two standard hoist capacities, I go for the larger one. For example, if my load is 3,500 lbs, I pick a hoist that can handle 4,000 lbs or more. It’s safer this way.
Diving Deeper: Factors to Think About
Average Load Conditions
I make sure the average load is around 50% of the hoist’s rated capacity. This keeps the hoist running smoothly and reduces wear.
Load Weight | Recommended Hoist Capacity |
---|---|
Up to 3,000 lbs | 3,000 lbs (1.5 tons) |
3,500 lbs | 4,000 lbs (2 tons) |
Safety Margin
I always add a safety margin. Usually, I multiply the load by 1.25 or 1.5. For example, a 2,000 lbs load needs a hoist rated for 2,500 lbs or more.
Duty Cycle
I think about how often I’ll use the hoist. For occasional use, a light-duty hoist is fine. But if I’ll use it every day, I go for a heavy-duty one.
Usage Frequency | Suggested Hoist Type |
---|---|
Rarely | Light-Duty Hoist |
Daily | Heavy-Duty Hoist |
Support Structure
Before I buy a hoist, I check if my beam or support structure can handle the load. It must be stronger than the hoist itself.
Planning for Future Needs
I also think ahead. If I might need to lift heavier loads in the future, I choose a hoist with extra capacity now. It saves me time and money later.
How I Ensure Safety in Hoist Operations
When it comes to hoist operations, I always prioritize safety. Over the years, I’ve learned some crucial steps that keep everything running smoothly and minimize risks.
Training and Certification
I make sure everyone operating a hoist is properly trained and certified. They need to understand the equipment, follow safety practices, and know what to do in an emergency.
Diving Deeper: Inspections and Safety Features
Pre-Operation Inspections
Before using a hoist, I inspect it thoroughly. This includes:
- Checking the hooks and latches.
- Examining chains or ropes for any wear.
- Testing limit devices and the operating mechanism.
Inspection Item | What to Check |
---|---|
Hooks and Latches | Cracks, wear, or damage |
Chains/Ropes | Frays, corrosion, or deformities |
Limit Devices | Proper functioning during operation |
Safety Features
I rely on built-in safety features like limit switches and emergency stop buttons. These features prevent accidents by stopping the hoist when something isn’t right.
Load Management
I never lift more than the hoist’s rated capacity. Overloading can cause equipment failure. For extra security, I use load limiters or overload protection systems.
Clear Work Area
I keep the area around the hoist clear. No one stands under the load, and I make sure everyone knows the hoist is in use.
Routine Maintenance and Emergency Plans
Regular Maintenance
I follow a strict maintenance schedule:
- Lubricating moving parts.
- Checking for wear and tear.
- Testing all safety mechanisms.
Maintenance Task | Frequency |
---|---|
Lubricate moving parts | Monthly |
Inspect safety features | Quarterly |
Emergency Preparedness
I always have a plan for emergencies. Everyone knows how to respond if equipment fails or if there’s an accident. Training sessions include practice drills for quick action.
Proper Rigging Practices
I attach loads carefully, ensuring slings and attachments are secure. I never allow the chain to rub against the load or hooks to tip.
How I Look at Reliable Electric Hoist Control Systems
I always start by checking if the system offers adjustable speeds. This helps me handle loads with more precision. For example, variable frequency drives (VFDs) let me slow down the hoist when I place a load, which avoids sudden jolts.
Diving Deeper: Safety Features and Voltage
Overload Protection and Limit Switches
I never skip built-in safety features:
- Overload protection stops the hoist if I lift too much weight.
- Limit switches keep the hook from traveling too far up or down.
Safety Feature | Purpose |
---|---|
Overload Protection | Stops operation when capacity is exceeded |
Limit Switches | Prevents dangerous over-travel |
Low Voltage Control
I also check if the hoist runs at a lower control voltage (like 24V or 120V). This lowers the risk of electric shock for me and my team.
Control Interfaces
I prefer a control system that responds fast. A pendant or remote control should let me raise, lower, and maneuver loads without delay. I need reliable buttons that don’t lag, so I can move heavy objects with steady accuracy.
Long-Term Durability and Feedback
Sturdy Construction
I want a system built to last. It should use high-quality parts to handle harsh environments. Regular inspections matter too. I schedule checks for wear, loose wires, and any sign of damage.
Maintenance Item | Frequency |
---|---|
Visual Inspection | Weekly |
Electrical Testing | Monthly |
Component Replacement | As Needed |
Feedback and Integration
Some systems have displays or signals that tell me about load weight or errors. If the hoist can link to sensors or extra safety gear, I feel more confident. This integrated approach keeps me informed and safe during every lift.
Why Lifting Equipment Safety Systems Matter
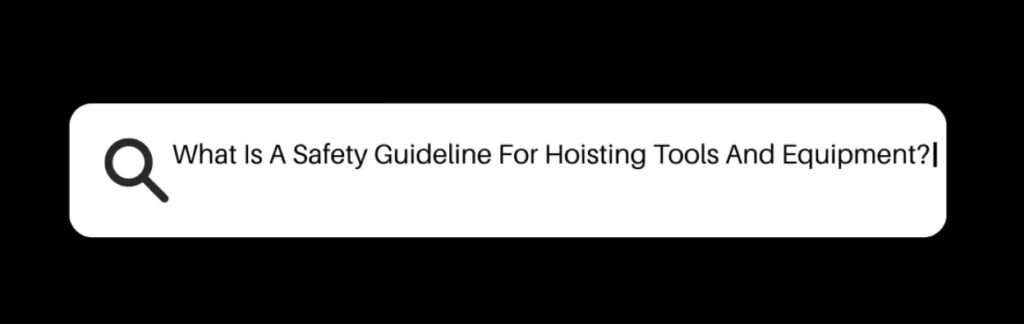
Lifting operations carry significant risks, from workplace injuries to equipment failure. Robust safety systems are essential for ensuring compliance, preventing accidents, and fostering a safer, more productive environment.
Lifting equipment safety systems minimize workplace risks, ensure compliance with standards like OSHA, and protect workers by integrating features like overload protection, regular inspections, and emergency protocols.
Imagine a lifting operation halted by equipment failure or injury—downtime mounts, risks escalate, and trust erodes. Let’s examine how safety systems prevent such costly scenarios.
Conclusion: How to Choose the Best Electric Hoist Control System for Your Lifting Operations
Choosing the best electric hoist control system is a critical step toward enhancing efficiency and safety in lifting operations. By focusing on key factors such as load capacity, lifting height, control type, and safety features, you can ensure the system aligns perfectly with your specific operational needs. Compatibility with your facility’s power supply and the hoist’s duty cycle further guarantees optimal performance and longevity.
Remember, a well-selected system doesn’t just handle heavy loads; it minimizes risks, boosts productivity, and fosters a safer working environment. Take the time to evaluate your requirements, consult reputable suppliers, and invest in a solution that delivers both reliability and value. With the right electric hoist control system, you can elevate your operations to new heights.